Этот проект позволил решить одну из давних заводских проблем и сэкономить солидные средства.
Благодарим редакцию газеты "Вести КАМАЗа" за предоставление данного материала.
Руководители и специалисты Центра информационных технологий и кузнечного завода реализовали проект, который позволил решить одну из давних заводских проблем и сэкономить солидные средства. Команде под руководством начальника отдела развития инфраструктурных решений Вадима Кузнецова удалось создать программу автоматического расчёта балансировки поковки коленчатого вала – сложнейшего продукта и визитной карточки предприятия.
Кроме портала, мы предлагаем вам и альманах «Управление производством». Все самое интересное и уникальное мы публикуем именно в нем. 300+ мощных кейсов, готовых к использованию чек-листов и других полезных материалов ждут вас в полном комплекте номеров. Оформляйте подписку и получайте самое лучшее!
Идею проекта принёс в команду ЦИТа главный специалист Алексей Мартюгин, во время работы на кузнечном заводе прорабатывавший её с начальником бюро конструкторского отдела инструмента и оснастки Ильсуром Харисовым. От правильной балансировки коленвала во многом зависит срок службы автомобилей, мощность, КПД и плавность работы двигателя. Необходимый уровень дисбаланса коленвала в первую очередь должен быть обеспечен на поковке. Именно из-за его отсутствия на заводе двигателей и на Ярославском моторном заводе невозможно было сделать качественную настройку на операциях механической обработки. Бывали случаи, когда дефект выявлялся перед финишной операцией – полировкой изделия, и тогда потери исчислялись солидными суммами.
Конструкторы и технологи КЗ постоянно размышляли над этой задачей. Несколько лет назад была приобретена установка, которая выявляет динамический дисбаланс вала и позволяет предотвратить отгрузку заводом заведомо бракованных поковок, что сокращает уровень потерь. Частично проблема была решена, но как нивелировать дефект полностью?
– Коленвал решили дорабатывать в тех местах, где это допускается делать, – вводит в курс дела начальник бюро конструкторского отдела инструмента и оснастки КЗ Ильсур Харисов. – Технологи Ярославского моторного завода определили места для дополнительной обработки, я в свою очередь сначала графически в программе AutoCAD, а затем с помощью Excel вычислял их значения. Ручной метод занимал колоссальное количество времени даже для подбора на один вал, при этом давая результат, далёкий от оптимального, но удовлетворяющий условиям балансировки на стороне потребителя.
Своя концепция была и у Алексея Мартюгина. Алгоритм решения проблемы он разработал ещё во время написания своей кандидатской диссертации «Совершенствование технологии изготовления поковок коленчатых валов с необрабатываемыми поверхностями», а использовал его во время работы над молодёжным проектом.
– Расчёт устранения дисбаланса оптимальным образом возможен только в специально созданной программе, которая за минуту способна проанализировать миллиарды комбинаций, – считает Алексей Викторович. – Для её создания по договорённости с руководством КЗ в ЦИКТе был выделен виртуальный сервер. Руководителям и специалистам пришлось немало потрудиться, чтобы завод получил максимально удобный для использования программный продукт. Просчитывали все возможные технологические схемы нивелирования дефекта в порядке их затратности в производстве, выбирали лучшую. Пользователям предлагались различные способы получения данных, как оперативные, доступные со смартфона на месте, так и возможность распечатки на бумаге для удобства стандартной работы на участке.
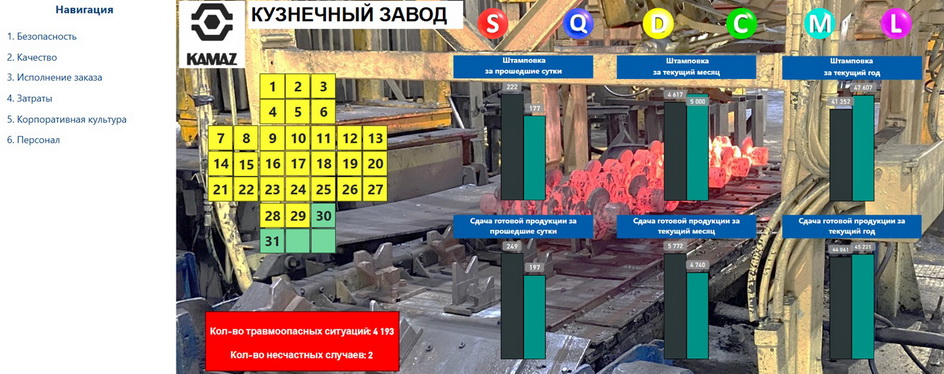
Активное участие в реализации проекта приняли и представители других служб КЗ. Тестирование, то есть доработку коленвала на фрезерном станке по полученным данным, делал станочник широкого профиля Рамиль Мугинов, который недавно дорос до инженера. Начальник бюро отдела контроля и анализа технологических процессов Вячеслав Балобанов курировал доработку поковок, получал обратную связь и агрегировал информацию от завода двигателей по результатам обработки, анализировал пользовательский опыт.
– Сейчас работники штампово-инструментального корпуса через смартфоны вводят в созданную программу данные с установки, которая измеряет векторы дисбаланса поковки, и автоматически получают результат с параметрами необходимой доработки, гарантирующей надлежащий дисбаланс, – поясняет руководитель проекта Вадим Кузнецов.
Благодаря автоматизированной программе расчёта доработки КЗ исключил брак по балансировке. Экономический эффект от внедрения проекта в несколько десятков раз превысил затраты на его реализацию. Он наверняка будет включён в топ-3 по итогам года. У молодых сотрудников компании есть шанс превзойти и этот блестящий результат. Реализуйте идеи, оптимизирующие производственные процессы, и вы получите премиальные выплаты и опыт, который не раз вам пригодится!
Татьяна Белоножкина. Фото: Виталий Зудин