Этот проект занял первое место в номинации «Разработка и освоение новых продуктов» на конкурсе по ПС имени А.Н. Моисеева.
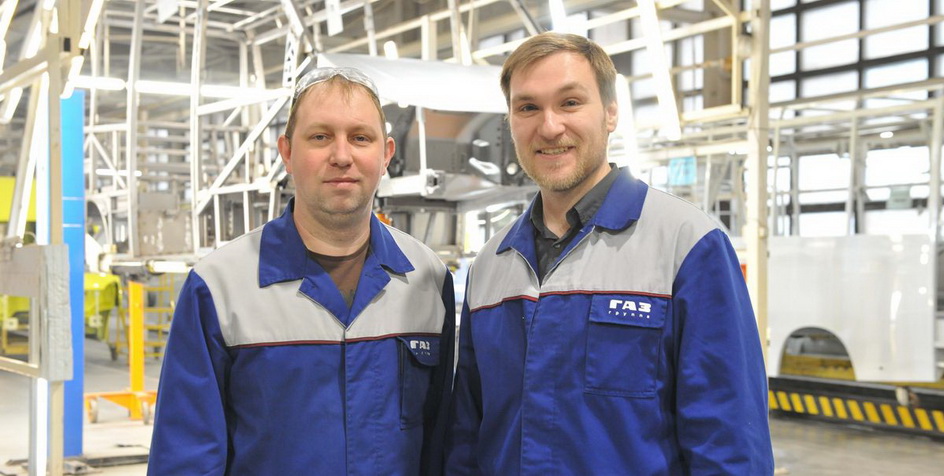
Проект стандартизированного участка деталей экстерьера автобуса «Газель CITY» воплотила команда дирекции по закупкам совместно с поставщиком из Набережных Челнов. Партнеры компании из самых разных сфер бизнеса все шире внедряют Производственную систему (ПС) «ГАЗ» в свою деятельность. Поставщику компонентов для автобусов «Газель CITY» она помогла успешно освоить новую технологию и повысить эффективность процессов.
Кроме портала, мы предлагаем вам и альманах «Управление производством». Все самое интересное и уникальное мы публикуем именно в нем. 300+ мощных кейсов, готовых к использованию чек-листов и других полезных материалов ждут вас в полном комплекте номеров. Оформляйте подписку и получайте самое лучшее!
Для увеличения объема выпуска, повышения качества и снижения стоимости комплектующих была внедрена технология получения деталей из SMC – композитного пресс-материала на основе стекловолокна.
– Это технология будущего, которая обеспечивает лучшее качество деталей по сравнению с привычным ручным формованием стеклопластика, – рассказывает один из ключевых участников команды проекта, ведущий специалист департамента по закупкам деталей интерьера и экстерьера Алексей Стрельчук. – «Газель CITY» – первый в России автобус, для которого из SMC изготавливают такие крупные и сложные компоненты, как боковые панели.
Изначально для автобуса поставлялись детали из стеклопластика ручного формования, трудоемкое изготовление которых влекло за собой высокую себестоимость. В связи с ростом объема сборки каркасных автобусов в производстве спецтехники (ПСТ) автозавода и большими перспективами продукта на рынке было решено освоить технологию получения деталей из SMC.
– В качестве нового поставщика мы выбрали предприятие в Набережных Челнах, которое одним из первых в России начало изготавливать компоненты из SMС для автомобильной промышленности, – говорит А. Стрельчук. – Однако, когда начали с ними работать, возникли вопросы по себестоимости, производительности и качеству. Тогда было принято совместное решение внедрить у поставщика Производственную систему.
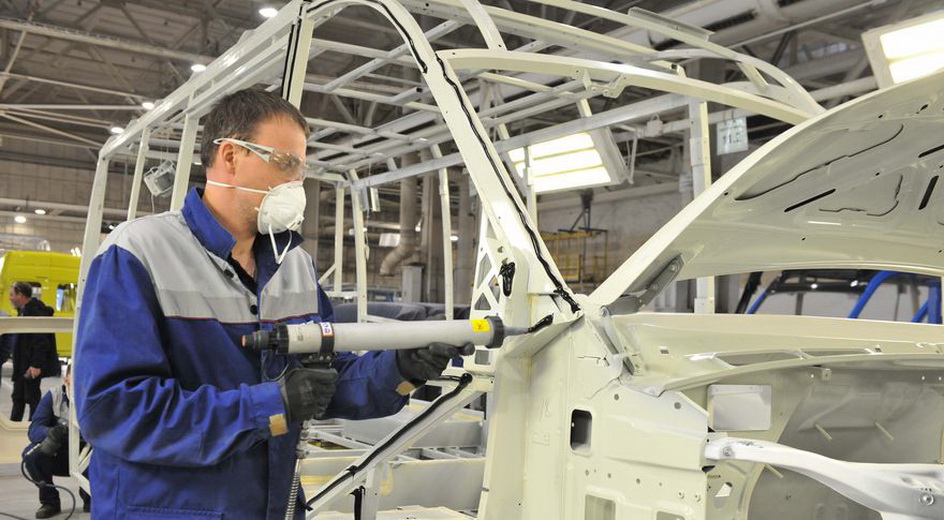
Плоды улучшений
– В рамках проекта специалисты дирекции по закупкам, я и Илья Алексеев, вместе с сотрудниками предприятия-поставщика внедряли кайзены, направленные на снижение трудоемкости процесса и себестоимости изделия, а наши руководители Никита Геннадьевич Буфалов и Валерий Иванович Кудасов совместно с коллегами из дирекции по развитию ПС оказывали нам консультационную и методологическую поддержку, – рассказывает А. Стрельчук. – Большой вклад в решение вопросов качества внес также главный специалист департамента по развитию поставщиков и обеспечению качества поставок нашей дирекции Сергей Шелипов. Была внедрена масса улучшений, стандартизирована работа операторов, изменена конструкция деталей, найден более качественный SMC-материал.
Одним из самых значимых кайзенов стало внедрение на участке прессования подвижного рабочего стола со встроенными автоматическими роликом и весами. Это позволило в два раза сократить потери в работе оператора, исключить колебания при нарезке и взвешивании материала.
– Это усовершенствование помогло правильно организовать производственный процесс на участке прессования, – отмечает А. Стрельчук. – Устранены ошибки при нарезке, сокращено количество отходов.
Благодаря ПС повысилось качество комплектующих, на 40% выросла производительность, снизилась трудоемкость процесса и цена деталей. Сокращение затрат от внедрения ПС за этот год составило 109 тыс. рублей, а экономический эффект от освоения SMC-деталей составил 35,04 млн рублей.
– Но главный результат проекта в том, что нам удалось успешно освоить передовую технологию, которая обеспечила нужные объемы, контролируемое и прогнозируемое качество по оптимальной цене. Ее можно применять и для других перспективных продуктов на всех заводах компании, – говорит А. Стрельчук.
Он подчеркнул, что сотрудники предприятия-поставщика проявили большой интерес к обучению инструментам ПС, содействовали всем новым начинаниям и помогли осуществить намеченные планы.
– Элементы бережливого производства мы пытались внедрять и раньше, но в рамках совместного проекта специалисты Горьковского автозавода помогли заметно ускорить этот процесс, – отметил руководитель проекта со стороны поставщика Сергей Зверев. – Наши сотрудники приняли нововведения буквально на ура, увидев, что их труд становится существенно легче. Без особых затрат усовершенствования дали серьезный эффект, производство вышло на новый качественный уровень. Все это стало приятным и неожиданным подарком от Горьковского автозавода, немногие компании готовы помогать своим поставщикам улучшать технологические процессы.
Результаты проекта не замедлили позитивно отразиться и на ходе сборки кузовов «Газелей CITY» на производстве спецтехники (ПСТ).
– Качество компонентов стало заметно лучше, доработки требуется намного меньше, повысилась стабильность поставок и сборки, снизилась трудоемкость, – говорит начальник участка цеха сборки автобусов Виктор Хлопунов. – Была сделана большая работа, поставщики приезжали к нам, мы вместе решали вопросы по качеству, с помощью специалистов вносили изменения в конструкцию. Разработали новую тару, которая обеспечивает транспортировку деталей без повреждений.
Инструкции, шаблоны и алгоритмы для старта проекта LEAN вы можете найти в практическом руководстве по внедрению бережливого производства.
В ногу со временем
Проект по созданию у поставщика стандартизированного участка занял в октябре первое место в номинации «Разработка и освоение новых продуктов» на конкурсе по ПС имени А.Н. Моисеева. Алексей Стрельчук участвовал в нем впервые, выступал с презентацией и очень рад успеху.
– Это мой первый проект в области ПС, с которой я ознакомился не так давно, но уже довольно близко соприкоснулся в рамках программы БС-250, где на деле научился применять ее инструменты, – говорит он. – В целом выступление на конкурсе прошло как надо, волновался только при объявлении результатов. Думаю, в победе нашей команды основную роль сыграли новизна технологии, а также смелые решения, которые мы принимали в ходе реализации проекта.
Полученный опыт А. Стрельчук уже использует при освоении деталей экстерьера из стеклопластика для производства автобусов нового поколения CITYMAX на Павловском и Ликинском автобусных заводах.
– Там применяется уже другая, совершенно новая для нас технология – пултрузия, которая обеспечивает идеально ровную поверхность крупных длинных профилей, – поясняет он. – Возможно, буду участвовать в конкурсе с новыми проектами.
Текст: Сергей Целибеев. Фото газеты «Автозаводец»