На конкурсе ОАК по совершенствованию производственной системы этот проект победил в секции «Сервисное обслуживание».
Благодарим Департамент корпоративных коммуникаций ПАО "Объединенная авиастроительная корпорация" за предоставление данного материала.
В цехе гальванических покрытий Комсомольского-на-Амуре авиационного завода (КнААЗ) им. Ю. А. Гагарина внедрен проект, который задействует установку термического дожига в отоплении помещений. Расходы на его реализацию быстро окупились с лихвой: эффект, и не только экономический, на предприятии в буквальном смысле почувствовали в первый же отопительный сезон. А проект в будущем может быть расширен.
Цех гальванических покрытий, еще когда возводился, задумывался как умное производство. На разных этапах технологического процесса было предусмотрено внедрение инновационных разработок, использование автоматизированного оборудования, а также сберегающих технологий. Эффективно использовать ресурсы – значит, снизить расходы, в том числе на энергопотребление. Это особенно актуально в условиях сурового климата Дальнего Востока: очень холодной, длинной зимы с 30-ти градусными морозами. Колоссальных энергозатрат требует не только масштабное производство, но и огромные заводские площади, которые должны быть комфортными для людей.
В Гальваническом корпусе КнААЗ, где на производстве работают более 150 человек, могли бы уместиться два футбольных поля и еще осталось бы место – площадь цеха 15 500 м2. Высота потолков достигает 18 м – фактически это высота шестиэтажного дома. Весь этот «объем» необходимо обогреть, в каких-то помещениях выдержать специальный температурный режим. Отопление обеспечивает заводская котельная, которая находится в 3 км от корпуса. Энергопотерь не избежать: при транспортировке тепла от котельной до цеха они составляли до 12 %. Но если представить, что расстояние не 3 км, а гораздо меньше, в десятки раз?
Кроме портала, мы предлагаем вам и альманах «Управление производством». Все самое интересное и уникальное мы публикуем именно в нем. 300+ мощных кейсов, готовых к использованию чек-листов и других полезных материалов ждут вас в полном комплекте номеров. Оформляйте подписку и получайте самое лучшее!
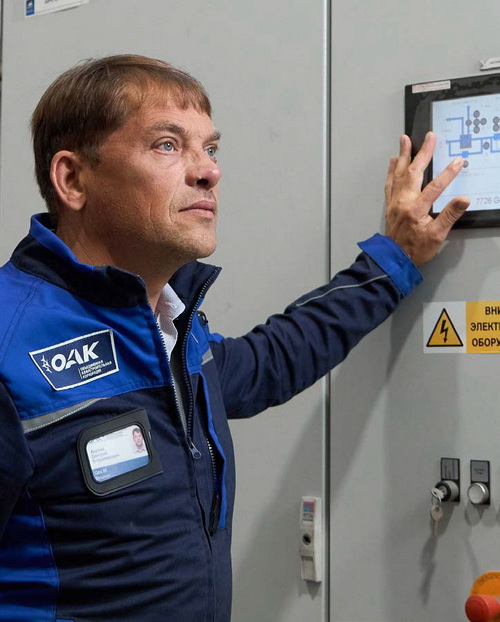
Дмитрий Акулин
Рациональный подход
Механик цеха Дмитрий Акулин предложил использовать тепло, выделяемое установкой термического дожига, которое фактически «уходило в трубу». Дело в том, что при сжигании вредных компонентов после выполненных операций образуется большое количество энергии. Раньше оно использовалось – всего лишь на 10 % – для предварительного нагрева воздуха, подаваемого зимой в малярные камеры. Однако, если тепла не просто много, а очень много, почему бы его не направить на отопление здания? «Теплообменный аппарат уже был, приточные установки тоже в цехе есть, работали за счет теплоснабжения от котельной, – рассказывает Дмитрий Акулин. – Три километра труб: при передаче тепловой энергии от котельной до гальванического цеха происходят неизбежные потери тепла. А при нагреве теплоносителя в корпусе цеха потери отсутствуют».
Проект разработали вместе с заместителем главного энергетика завода Михаилом Овчаровым. Рассчитали, сколько понадобится на монтаж труб от теплообменного аппарата до приточных установок, а также на наладочные работы. Рабочая группа выверила экономическую целесообразность. Всего подключить к собственной «термической котельной» решили четыре участка: приготовления и хранения красок и два отделения очистных сооружений, в общей сложности 9504 м3. Вроде немного, но есть нюансы. «Очистные сооружения – это помещения внушительных размеров, плюс высота потолков метров по 10, – объясняет Михаил Овчаров. – Когда помещение по объему большое, нужно много отопления. Серьезный объем воздуха, который надо обогреть. На участках лакокрасочных материалов строгий температурный режим и очень мощные вытяжки: теплообмен происходит крайне интенсивно – это тоже вопрос к энергозатратам. Представьте, например, что вы зимой поставили тепловую пушку в гараже и при этом открыли нараспашку дверь – то же самое получается в помещении приготовления лакокрасочных материалов: большой воздушный поток, который все время гуляет».
Затраты на проект – 1 миллион 154 тысячи рублей – окупились в течение одного отопительного сезона. Экономия каждый год – почти 3 миллиона рублей. Столько тратилось на тепло от заводской котельной. На конкурсе ОАК по совершенствованию производственной системы этот проект победил в секции «Сервисное обслуживание».
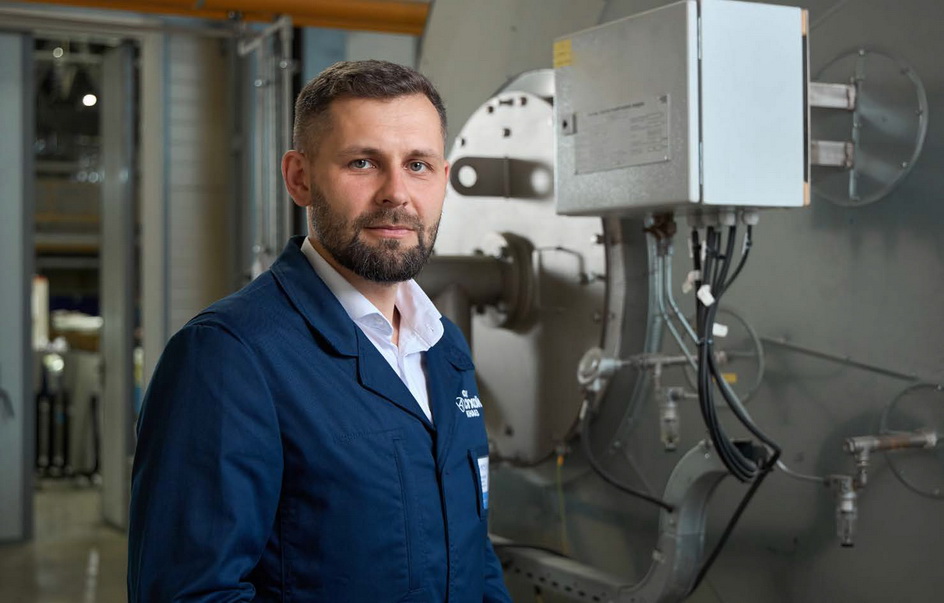
Михаил Овчаров
Не считая градусы, экономить рубли
«Главное – людям комфортно, хоть 30 градусов можно сделать», – говорят участники проекта. При том что температура в помещениях регулировалась и раньше (нормы СанПиН на заводе строго соблюдаются), дополнительный градус оборачивался «потраченным рублем». Теперь теплее не значит дороже. «Мы подходим к энергетике скрупулезно, и у нас каждый градус на счету, – отмечает Михаил Овчаров. – А здесь установка все равно вырабатывает дополнительную энергию. Когда мы подключались, делали расчет, чтобы тепловой режим в помещении был в оптимальном диапазоне при максимально низких температурах, то есть при минус 35-40, у нас полностью выдерживала система отопления. Соответственно, если на улице 25 градусов мороза, в этой установке есть цеховой запас. Подразделение может само регулировать диапазон температур. Побольше-поменьше».
Максимальная отдача
В будущем к «термической котельной» могут подключить и другие участки цеха. «Если в установку внедрить более мощный теплообменник, – говорит Дмитрий Акулин, – сможем, наверное, отапливать весь гальванический корпус. Кроме того, теоретически тепловую энергию можно преобразовывать в электрическую. Но это еще предстоит все додумать».
К ресурсосбережению на предприятии особое внимание. К примеру, помимо использования тепла, которое вырабатывается установкой термического дожига, применяется замкнутый цикл потребления воды, то есть ее повторное использование. Метод выгодный – с точки зрения экономии, важный – для экологии. «Вода поступает в цех, подготавливается специальным образом, затем направляется в промывочные ванны, оттуда возвращается на очистные сооружения, очищается, добавляется примерно около 30 % вновь подготовленной воды, и опять происходит возвращение, – рассказывает Жанна Петровская, начальник цеха гальванических покрытий. – При этом воду, которая очищается, мы также можем сбрасывать в канализацию, так как она уже не содержит в себе вредных веществ».
Сейчас воплощается новый проект: работают над системой кондиционирования, чтобы охлаждать помещения летом. По аналогии с «термической котельной» точно так же задействуют имеющиеся установки – на этот раз холодильные. В жаркое время они подают в малярные камеры прохладный воздух. Мощность установленных компрессоров такова, что ее хватит на «климат-контроль» практически всего гальванического цеха.
СПРАВОЧНО
Дожиг против выбросов
Термический дожиг используют во многих отраслях: в нефтехимической, химической, пищевой, сельскохозяйственной, стекольной, деревообрабатывающей промышленности. Без таких установок не обходятся тепловые электростанции, малярные цеха, полиграфические предприятия и заводы по переработке кофе, где на производстве вместе с волшебным ароматом напитка, с которого у многих начинается утро, присутствуют загрязняющие атмосферу вещества. С помощью дожига выбросы как раз очищают от примесей, минимизируя содержание вредных веществ после выполнения различных технологических операций. Такое обезвреживание проводится при очень высоких температурах: обычно от 750 до 1200 °С. Термический дожиг позволяет достичь 99-процентной очистки выбросов – даже при высокой концентрации вредных соединений. Экологическая сторона этого процесса понятна – в атмосферу выходит не токсичный, а очищенный горячий воздух. С помощью специального теплообменного устройства его можно использовать в отопительной системе, уменьшив энергозатраты.
Начальник цеха гальванических покрытий КнААЗ им. Ю. А. Гагарина Жанна Петровская рассказывает: «У нас осуществляется несколько технологических процессов: это анодирование алюминия, размерное химическое травление алюминия, размерное химическое травление титана. Сейчас мы запускаем два новых процесса для нашего цеха – анодирование титана и осветление титана после термообработки. Также выполняется окрашивание деталей согласно конструкторской документации различными грунтовками и эмалями… Установка термического дожига очищает загрязненный воздух из малярных камер. Сначала он проходит через фильтр твердых частиц, далее – через цеолитный наполнитель, затем это все поступает в камеру сжигания, где происходит окисление отработанного воздуха под действием высокой температуры. Раньше очищенный горячий воздух выводился в атмосферу. А сейчас идет на отопление помещений».
Текст: Инна Жебари. Фото ОАК