Почему внедрение процессов ТОиР необходимо начинать с этапа проектирования, какие бенефиты для предприятия дают HAZOP-сессии в реальной производственной практике и кто виноват в отказе оборудования — человек или система. Артур Черехович, начальник управления по безопасности и эффективности производственных процессов Иркутской нефтяной компании, поделился своим видением организации процессов управления активами с Романом Пилькиным, генеральным директором Деснола, российского центра практической экспертизы по цифровой трансформации ТОиР.
О разнице в подходах
Роман Пилькин: Артур, каким был ваш путь в сфере технического обслуживания и ремонта (ТОиР) оборудования, и какой свой профессиональный опыт вы считаете наиболее значимым?
Артур Черехович: В ТОиР я пришел из эксплуатации. Вся моя профессиональная жизнь связана с нефтегазовой отраслью, и начинал я свой путь как инженер добычи. Работал в иностранных компаниях как в России, так и за рубежом. Мне посчастливилось пройти, наверное, все стадии жизненного цикла продукции, кроме утилизации производственных объектов. Выстраивал процессы с нуля: принимал оборудование от поставщика, формировал команду. Можно сказать, побывал и по ту, и по другую сторону баррикад, а сейчас занимаюсь уже не столько производственной деятельностью, сколько вопросами, связанными с повышением эффективности процессов.
Роман Пилькин: По вашим наблюдениям, отличаются ли подходы к ТОиР в России и за рубежом?
Артур Черехович: Есть отличия в разнице подходов, хотя сейчас многие грани и стираются из-за того, что мы заимствуем практики из так называемого западного менеджмента. В России подход более персонифицированный. У нас ошибка оборудования обычно воспринимается как недоработка сотрудника, который несет за него ответственность. На Западе же отказ оценивают как сбой системы.
Роман Пилькин: Получается, в западных практиках линейный сотрудник может быть причастен к проблеме, но не может быть ее причиной?
Артур Черехович: Ну, наверное, в каких-то крайних случаях может быть и причиной, если речь идет о совсем уж откровенном саботаже или умышленном вредительстве. Но в основном, да, в передовых западных компаниях упор делается на то, чтобы найти дыру в системе.
Если человеку не хватает знаний, значит компания должна организовать для него обучение. Если он выполняет не те операции, значит необходимо дать ему актуальную технологическую карту ремонтного процесса, где будут также прописаны необходимые ресурсы, инструменты и запасные материалы.
Искусство планирования
Роман Пилькин: Компания приступила к цифровизации ТОиР еще десять лет назад, а сейчас, как я понимаю, ТОиР занимает все более значимое положение в экономике предприятия. Какие цели и задачи этого направления являются наиболее важными в ближайшей перспективе?
Артур Черехович: Моя деятельность в ИНК заключается в повышении эффективности и безопасности производственных процессов. Изначально меня пригласили в компанию для развития системы PSM (Process Safety Management), то есть системы управления технологической безопасностью.
Очень важная задача сегодня — внедрить более четкое календарно-сетевое планирование ТОиР для снижения потерь, связанных с несогласованностью действий ремонтных и сервисных подразделений. Речь идет о ситуациях, когда, например, бригада приезжает на объект выполнять некую работу, а технологический транспорт, необходимый для ее проведения, уехал на другую площадку. Исключить такие ситуации возможно за счет выстраивания четкой приоритизации, чтобы каждый понимал, что нужно делать в первую очередь, а что может и подождать. Расстановка приоритетов зависит от степени риска. На что может повлиять то или иной событие: снижение финансовых показателей, жизнь и здоровье людей, экологическую обстановку, репутацию компании. В зависимости от этого мы и расставляем приоритеты.
Сейчас мы переживаем второй этап развития системы ТОиР. Период первоначального внедрения, как вы правильно сказали, был в 2014 г. В данный момент мы делаем акцент на формализацию базового оборудования и нормативов, а также серьезно дорабатываем софт, чтобы он поддерживал бизнес-процессы, которые мы внедряем на производстве. Также мы проводим большую работу по интеграции 1С:ТОИР КОРП от разработчика и интегратора Деснола, с которой мы уже сотрудничаем десять лет, с системами управления материально-техническим обеспечением, складским хозяйством, автотранспортом.
Роман Пилькин, CEO Деснола
Каким будет упущенный маржинальный доход
Роман Пилькин: А если объект новый, и оборудование еще не эксплуатируется?
Артур Черехович: Тогда основным фактором является критичность. У нас определены четыре степени критичности в зависимости от того, каким будет упущенный маржинальный доход при отказе той или иной единицы оборудования. И, соответственно, в зависимости от этого происходит ранжирование, выбор определенного анализа.
Для оборудования и узлов с наивысшей степенью критичности мы применяем RCM-анализ (Reliability Centered Maintenance — обслуживание, направленное на обеспечение надежности оборудования и оценку рисков в безопасности и производстве). Далее идут FMEA/FMECA, (Failure Mode and Effects Analysis — анализ видов и последствий отказов, Failure Mode Effective Criticality Analysis — анализ видов, последствий и критичности отказов), техническое обслуживание по состоянию и работа до отказа. Для тех случаев, когда дефект уже случился, мы также используем нашу матрицу оценки рисков, адаптированную под ТОиР. Там, соответственно, вопросы очень простые: «А что случится, если ничего не делать, и когда это случится?».
Эта приоритизация автоматически дает нам срок устранения данного дефекта, и для инженера по планированию он становится маяком, определяющим, куда ставить работу. Есть дата, раньше которой нет смысла начинать ремонт, есть целесообразный срок, и есть критическая отметка. В том, чтобы попасть в нужный диапазон с каждым узлом и с каждой единицей оборудования и заключается искусство планирования.
Роман Пилькин: А какую часть оборудования у вас охватывает RCM-анализ, и как много у вас ресурсов на это тратится?
Артур Черехович: Сейчас эта практика у нас находится в процессе внедрения, и, конечно, ресурсов хотелось бы больше. Часть инженеров-надежников уже обучена этому методу, другие только его изучают. Что касается покрытия, то, я думаю, это около 10–15% оборудования наивысшей степени критичности. Учитывая, что RCM-анализ — процесс крайне трудоемкий и затратный, распространение его на все узлы и агрегаты было бы неэффективным использованием ресурсов.
Роман Пилькин: Случились ли у вас какие-то инсайты по итогам RCM-анализа, поменялись ли подходы к обслуживанию оборудования на основании полученных данных?
Артур Черехович: Да, например, мы решили перепроектировать отдельные производственные участки, поскольку изначальный проект не обеспечивал нужный нам уровень безопасности и надежности. Где-то мы добавили дополнительные плановые работы, а где-то перешли на обслуживание по фактическому техническому состоянию. Возможно, это не было прямым следствием RCM-анализа, но мы увидели, что часть плановых работ, предписанных производителем, избыточна, и их можно оптимизировать, руководствуясь принципом «работает — не трогай».
Также RCM-анализ помог нам сформулировать требования к страховому запасу и сформировать перечень запасных частей, которые нужно всегда держать на складе для минимизации крупных отказов.
Наибольший эффект от HAZOP
Роман Пилькин: Помимо RCM-анализа, какие еще инструменты технологической безопасности вы применяете?
Артур Черехович: Для оценки состояния как текущего, так и нового оборудования у нас очень активно применяются HAZOP-сессии (Hazard and Operability Study — анализ опасности и работоспособности).
Смысл HAZOP заключается в том, что система делится на определенные узлы, которые фасилитатор сессии оценивает с применением слов-модификаторов. Например, давление — больше оно стало или меньше? По какой причине это произошло? Какие будут последствия? Защищены ли мы от возможных проблем? Как правило, в результате этих сессий мы находим то, что раньше не досмотрели, не досчитали. И если у нас в реальности происходит отказ, то мы всегда можем вернуться назад и посмотреть, учитывали ли мы его на стадии HAZOP, RCM или любой другой методики.
Роман Пилькин: А на стадии создания нового производства вы тоже проводите для оборудования такие сессии?
Артур Черехович: Наибольший эффект от HAZOP получается именно на том оборудовании, которое еще не эксплуатируется. Изменения на этапе чертежа обходятся компании намного дешевле, чем в железе. К тому же, есть возможность привлечь к сессии и проектантов оборудования.
Также я хотел бы обратить внимание, что проектирование проекта — это и начало подготовки к ТОиР данного объекта, поэтому мы подключаем представителей ТОиР к оценке готовности оборудования к дальнейшей эксплуатации. Здесь очень эффективны 3D-модели. Я сталкивался с ситуацией, когда из теплообменника невозможно было вытащить трубный пучок из-за того, что рядом располагалась капитальная колонна здания. Уже можно представить стоимость устранения этой недоработки. Такие вещи легко отследить и скорректировать еще на этапе 3D-моделирования. И у нас это связано с соответствующим программным комплексом и системой 1С:ТОИР КОРП. Есть даже специальные алгоритмы автоматической проверки доступности оборудования, его готовности к техническому обслуживанию.
Кроме того, чтобы обеспечить эксплуатационную готовность, мы заранее заполняем базы данных, в том числе по запчастям, инструментам, приспособлениям. И очень важно, чтобы люди, которые потом будут эксплуатировать оборудование, подключались к пуско-наладочным работам, ведь у них совершенно другой интерес и другой фокус внимания.
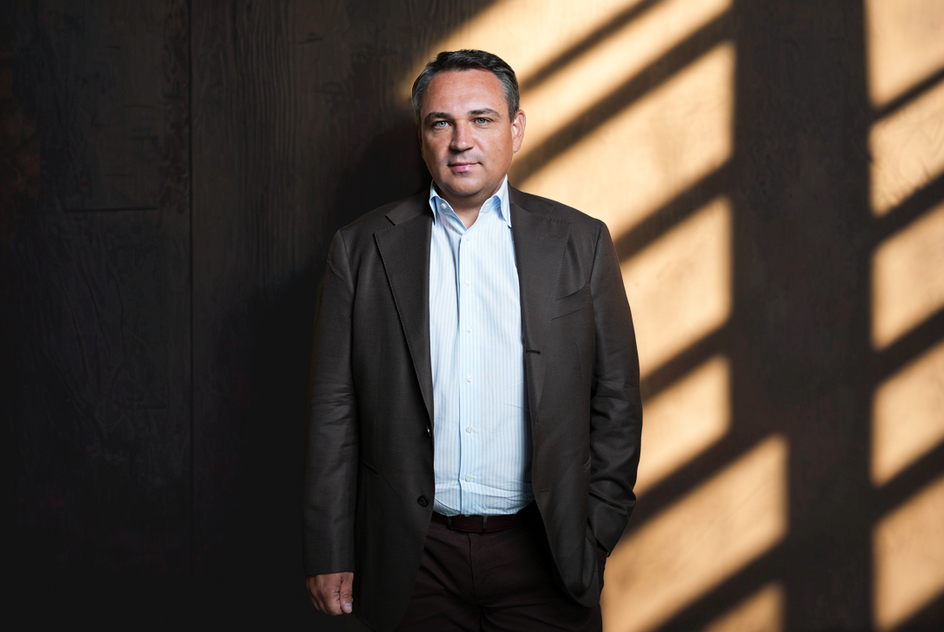
Артур Черехович, начальник управления по безопасности и эффективности производственных процессов Иркутской нефтяной компании
Где системный сбой
Роман Пилькин: В ИНК вы управляете безопасностью и отвечаете за эффективность производственных процессов. Какова связь между двумя этими областями, и как одна влияет на другую?
Артур Черехович: Технологическая безопасность базируется на трех китах. Это проектная, эксплуатационная и техническая целостность. Проектная целостность представляет собой совокупность всех технических решений, которые закладываются в проект. И здесь наша задача заключается в том, чтобы в дополнение к существующим законодательным требованиям, которые есть в России, добавить какие-то свои наработки, обеспечивающие безопасную и эффективную работу оборудования.
Эксплуатационная целостность тоже напрямую связана с ТОиР. Потому что, например, дефекты и неисправности обнаруживает не только ремонтный, но и эксплуатационный персонал. И это еще одно направление, которое мы хотим активно внедрять, чтобы разгрузить ремонтные подразделения.
Но чтобы это работало, надо повышать эффективность обходов. Для этого мы разделили производственные площадки на зоны, чтобы каждый сотрудник отвечал за определенное оборудование, а также разработали визуальные презентации — стандарты проактивного мониторинга. По ним люди понимают, как выглядят дефекты. Это позволило привлечь внимание к вещам, которые раньше не попадали в поле зрения операторов, и в итоге мы получили прямо-таки галопирующий рост зафиксированных дефектов.
Роман Пилькин: А как вы работали с персоналом, чтобы у людей не было отторжения новых для них функций и задач?
Артур Черехович: Во-первых, мы всегда объясняем, для чего мы это делаем, и часть отторжения снимается уже на этом этапе. Но только часть. Во-вторых, у нас есть система мотивации. Например, если отказ происходит в зоне ответственности сотрудника, и он мог его визуально определить, то это минус от премии, если отказов не было, то плюс.
Кроме того, очень важна поддержка со стороны топ-менеджмента. Когда линейный специалист видит, что руководитель заинтересован в решении вопросов, он сам тоже начинает проявлять инициативу. Это хорошо и для предприятия, потому что обычно полевые руководители не склонны транслировать производственные проблемы, в итоге они консервируются и не решаются, а здесь мы сразу находим системный сбой. Хочу подчеркнуть, что важно именно найти проблему, устранить ее и сделать так, чтобы она не повторялась в будущем, а не назначить виноватого. Это самая главная тема, которую пока тяжело преодолеть.
Роман Пилькин: Как раз такой подход и позволяет каждую ошибку рассматривать исходя из того, что мы можем улучшить в системе?
Артур Черехович: Да, и нам тоже приходилось с этим сталкиваться. Предположим, человек совершает ошибку, а, в соответствии с должностной инструкцией, он не должен был ее допустить. Но мы все прекрасно понимаем, что, когда сотрудника нанимали, никто не проверял, обладает ли он полным набором необходимых навыков и компетенций. Тем не менее, его допустили к работе. Соответственно, это компания совершила ошибку, не обучив работника, не проверив должным образом его знания. Поэтому очень важно выстраивать на предприятиях систему корпоративного обучения, чтобы и у работодателя было реальное понимание уровня подготовки персонала, и сотрудники осваивали именно те компетенции, технологии и направления, которые будут приумножать ценность компании.
Источник изображений: пресс-служба Деснола
Хотите узнать, как повысить эффективность службы ТОиР? Запишитесь на бесплатный разбор вашей службы ТОиР по ссылке и получите 10 полезных материалов для технического директора в подарок
Реклама ООО «Деснол Софт Проджект» ИНН 7709568068 ОГРН 1047796704878