На Горьковском автозаводе расширили сферу применения внутрицеховых транспортных роботов.
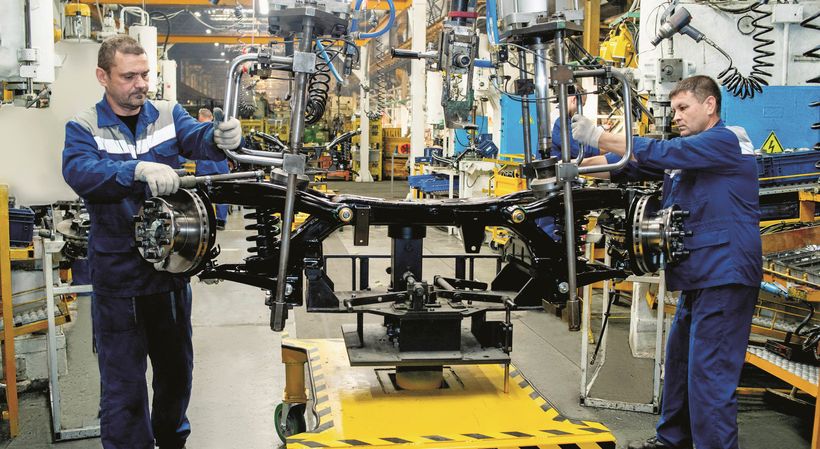
Новые маршруты
Всего год назад первые диковинные роботы-транспортёры появились в цехе сборки грузовых автомобилей. Теперь сеть беспилотных маршрутов как паутина опутала весь корпус. Юркая платформа уже привычно снуёт по цеху, доставляя детали на сборочный конвейер. Роботы едут со скоростью 4 км/ч, ориентируясь по магнитной полосе с RFID-метками. С помощью лидаров они могут различать препятствия на своём пути, при их появлении роботы останавливаются и сигнализируют о них. А ещё транспортёры умеют регулировать очерёдность: если, например, тележка находится на выгрузке кабины, она сообщает следующей за ней по Wi-Fi, что место занято, и та останавливается в определённой точке.
Кроме портала, мы предлагаем вам и альманах «Управление производством». Все самое интересное и уникальное мы публикуем именно в нем. 300+ мощных кейсов, готовых к использованию чек-листов и других полезных материалов ждут вас в полном комплекте номеров. Оформляйте подписку и получайте самое лучшее!
Вот один из роботов подъезжает к участку «супермаркет». Сотрудник экспедиции Татьяна Лопухова загружает тару фарами и щелчком мыши отправляет её на конвейер. На мониторе видна вся производственная логистика – к примеру, на четвёртый конвейер только что доставили зеркала для «Газона NEXT», а с первого поступил запрос на жгуты проводов.
– Для подготовки новых беспилотных маршрутов мы расширили проезды между конвейерами, сузив ячейки сборки радиаторов и сидений и почти на метр переместив вспомогательные колонны, поддерживающие антресоль цеха. Оборудовали даже «парковочные карманы», чтобы в процессе разгрузки роботы не занимали место на дороге, – говорит главный специалист по ПС Светлана Коробейникова.
Напомним, год назад всё началось с того, что на линию вышли три транспортных модуля, каждый из которых мог перевозить на конвейер по одной кабине автомобиля «Газель».
– Освоив первый маршрут, мы начали думать о том, как оптимизировать его ещё больше, ведь грузоподъёмность роботов позволяет перевозить сразу две кабины. В этом вся суть философии Производственной системы, которая учит нас быть в постоянном поиске новых идей, – вспоминает Светлана Коробейникова. – Сколько экспериментов провели! У нас девять типов кабин, надо было разместить их на тележке в подходящем положении для подъёмного устройства. Протестировали 18 возможных вариантов – ставили все кабины в паре друг с другом, каждую проверяли в нескольких позициях, и наконец нашли оптимальное расположение.
Сегодня в цехе сборки внедрён уже 21 беспилотный маршрут, они обслуживают 173 потока подачи комплектующих.
Сделано у нас
Компания не просто расширяет сеть беспилотной логистики, но и создала собственные умные транспортёры, которые выпускают в Нижнем Новгороде. Корпуса для самоходных тележек изготавливаются в производстве спецтехники; валы, втулки, шпильки, кронштейны и другие мелкие детали – на заводе штампов и пресс-форм. Сборка, наладка и обкатка роботов ведутся на специальном участке в цехе сборки автомобилей.
– Здесь у нас и производственная площадка, и испытательный полигон, – показывает участок сборки автоматически управляемого транспорта Алексей Грубов, начальник отдела промэлектроники.
На ста «квадратах» есть зона сборки, кабинет, в котором разрабатываются программы маршрутов и визуализация движения беспилотников. На полу – магнитные ленты для «дорожных испытаний». На столе лежит полуразобранный робот-транспортировщик.
– Это учебный экземпляр, с которым работают специалисты цехов, где только готовятся к цифровизации внутрицеховой логистики. На нём мы и сами тренируемся, когда разрабатываем новую программу или вносим изменения в конструкцию. Перед вами модификация с двумя захватными устройствами, с помощью которых роботы могут перевозить больше номенклатуры, – говорит Алексей.
Среди перспективных разработок – робот-транспортировщик с так называемой SLAM-системой, который сможет работать в тандеме с автоматической линией сварки кузовов и объезжать препятствия на своём пути. Также в 2025 году, по словам Алексея Грубова, планируется создать более манёвренные роботы малых размеров для перевозки рам и мостов, которые смогут перемещаться задним ходом.
Альтернатива конвейеру
На заводе мостов и агрегатов (ЗМА) сотрудники дирекции по развитию Производственной системы «ГАЗ» пошли ещё дальше и нашли роботам-транспортёрам новое применение на участке стапельной сборки передней подвески «Газели NEXT».
Раньше рабочие вручную толкали стапельные тележки между пятью последовательными станциями сборки. На это операторы тратили до четырёх часов в сутки, т.е. 20% своего рабочего времени.
– С одной стороны, у нас была излишняя численность, с другой – неравномерная загрузка, поток не был синхронным, что влияло на ритмичность сдачи готовой продукции, – вспоминает главный специалист по Производственной системе Александр Мосалёв. – Мы стали искать нестандартные пути, чтобы расшить узкое место. Робот-транспортировщик – это отличное решение!
Для этого пришлось разработать новую конструкцию стапельной тележки, с которой мог бы состыковываться робот-тягач, подготовить инфраструктуру на заводе мостов и агрегатов – выполнить наливные полы, нанести магнитную ленту, обеспечить Wi-Fi-покрытие и провести перемонтаж потока под внедрение новой техники.
Огромную поддержку команде проекта оказал директор дивизиона «Автокомпоненты» Виктор Кадылкин. Сотрудники «Центра ИТ-решений для бизнеса» провели подключение серверов и установку контроллеров. Дневали и ночевали на площадке ЗМА специалисты в области беспилотной логистики из ПГА: помогали разрабатывать трассировку, наносить магнитную ленту, первую стапельную тележку испытывали на маршруте вдоль 4-го конвейера, после чего вносили необходимые улучшения. Наконец в июле начались испытания на участке сборки передней подвески «Газели NEXT» в ЗМА.
Сегодня здесь организован полноценный участок с маршрутом движения протяженностью около 60 метров, на котором перевозку тележек от станции к станции осуществляют пять роботизированных тягачей.
Принять участие: проект «Цифровое производство»
– Когда мы начинали изменения, операторы лишь смеялись: «Да не поедет оно! 10 лет толкали тележки и столько же будем толкать». Но сейчас они нас благодарят, ведь теперь их труд стал намного легче. Поток синхронизирован, то есть люди занимаются исключительно той работой, что приносит ценность продукту. Автоматизация влияет и на отношение новых сотрудников. Недавно, например, на ЗМА пришёл молодой парень по временному договору и так впечатлился нашими роботами, что попросился в штат на постоянную работу, – говорит Александр Мосалёв. – Мы с удовольствием его приняли.
Видео о том, как на Горьковском автозаводе работают транспортные роботы, смотрите здесь
Текст: Татьяна Лякина, Максим Карпухин. Фото «Время машин»